Voices of the stakeholders
Interview with Ing. Mirela Tricomi Ursuleac
Head of Special Processes Competence Center and Welding Coordinator 1° level in Ansaldo Energia
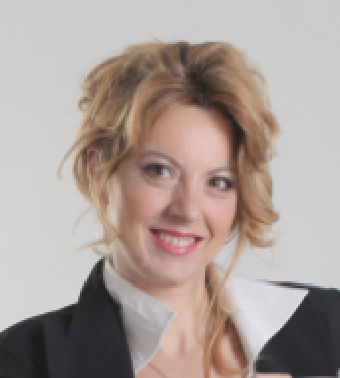
On which products have you focused the Lighthouse Plant project concerning additive technology?
As Team Leader I manage one of the many objectives of the LHP project, which concerns the definition of a qualification path for our suppliers who realize, with the Power Bed Fusion technology, gas turbine hot parts components. The chosen components perform "mission critical" tasks in the performance of the machine and have very complicated geometries. The activities are divided into 4 Milestones and include a deepening of the regulatory and scientific support in the field of additives, the definition of a qualification plan with experimental laboratory tests to arrive at the definition of a special process qualification specification. To date, the components that make the case for our experimental study are manufactured in the production departments of our suppliers.
What is the main objective of the team in this specific project?
Through laboratory tests, in collaboration with Genova Additive Manufacturing Laboratory, it is necessary to identify the optimal essential parameters of the machine in order to obtain a production of almost net-shaped components with characteristics according to the design. By means of laboratory tests, the optimal essential machine parameters are identified in order to obtain a production of near net shape components with metallurgical structural characteristics according to the project. Therefore, the ability to identify the causes of the defects created by the process and take appropriate corrective action to avoid repetition can be a great contribution in developing advanced and intelligent AM systems, and in reducing the cost of non-quality. In the figure there is one of the jobs representing the production components that will be built taking into account the type of material, dimensions, geometries, class of use of the component and risk category. The jobs will provide important data on the repetitiveness of the process through laboratory tests that will evaluate the characteristics of the powders (chemical composition, granulometry, melting point, etc...), identify the optimal machine parameters and verify the mechanical and metallurgical properties, structural continuity with mapping of any defects, surface finish and dimensional conformity.
How do you put this project into your strategy?
The final objective of the project is to define a qualification specification that serves as a guideline for the qualification activities of our Suppliers that produce with additive technology. This is part of our company's strategy to acquire full control of this new process, which is now largely entrusted to our Suppliers, with the benefit of improving the quality of our components. The transfer of knowledge in the field of high technology from the academic world to our production reality is a path characterized by a starting point that is research and a point of arrival that is the market and has as a unit of measure the degree of customer satisfaction. To this end the specific AMiCE network interaction is producing interesting insight as clarified also by Prof. Fabrizio Barberis, Vice Coordinator of University of Genoa Technology Transfer Commission in his interview for the AMiCE Project.
In order to increase skills in the field of high technology, it is essential to transfer knowledge from the academic world to our production reality, which is nothing more than a path characterized by a starting point that is research and a point of arrival that is the market. The technological maturity of a company leads to greater flexibility, speed and quality of services and is always measured by customer satisfaction.
More information:www.ansaldoenergia.com