Voices of the stakeholders
Interview with Henry Burkhardt, Oliver Bumbel and Paul Blankenstein
IHD Institute for Wood Technology Dresden
Test geometry produced with selective hot presses - 20 layers of spruce chips mixed with thermoplastic binder
Which tasks and goals do you pursue as an employee of the IHD Dresden?
Oliver Bumbel:
My name is Oliver Bumbel and I work in the field of furniture production and processing of wood-based materials. With regard to various feasibility and sustainability studies, we look at different technologies and manufacturing processes for furniture production.
Paul Blankenstein:
My name is Paul Blankenstein, also from the furniture and interior design sector, working among other things in the field of generative manufacturing. Within the scope of various projects, the production of novel or more efficient furniture components, but also building elements, is examined.
Paul Blankenstein:
Henry Burkhardt is my name and I work in the materials department at the IHD Dresden. My focus is in the field of materials development as well as technology development and optimization, i.e. to transfer technologies from the wood material industry into additive manufacturing processes.
Which projects in the field of additive manufacturing are you currently working on at the IHD Dresden?
Oliver Bumbel:
"3D FeSy" - this project is about finding alternatives to conventional manufacturing processes and spring systems by means of generative manufacturing. According to the laws of integral construction in additive manufacturing, the component consists of different strengths on a vertical as well as horizontal level. This means that different suspension properties can be achieved in seat upholstery, depending on the depth and width. To this end, different approaches are tested, for example the material properties by using different elastic materials. The design of the component using different wall thicknesses and widths also plays a decisive role in the testing of elastic structures.
Henry Burkhardt:
The project "Generative Manufacturing Wood +" pursues the approach to increase the proportion of wood in generative manufacturing to about 90%. For this purpose, three concepts for the transfer of the active principles from the wood-based material production to the additive manufacturing process were developed. The first concept consists of selective hot pressing, i.e. to create a component, the powder bed is compressed into a solid body without the detours of a melting process. The second concept consists of selective gluing. Similar to the PolyJet process, a binding agent is applied to the powder bed and particles are bonded together using a hot pressing process. The third concept is based on the extruder process Fused Filament Fabrication, with 90% wood and thermoplastic components. For this, the method of depositing must be newly developed and appropriate thermoplastic binders must be found. The project was completed at the end of 2019 - whereby selective hot pressing proved to be the most successful and the first objects were produced. In addition, during the AMiCE info session in Zittau, new findings regarding thermoplastic binders and synergies were formed.
What perspectives and special fields of application do you see for additive manufacturing in the future?
Paul Blankenstein and Henry Burkhardt:
A big progress would be the reduction of the binder content in wood 3D printing. There are research applications that only use and extrude wood and wood components - thus material research can be advanced and recycled at the same time. In addition, in the future a focus could be on materials research, for example in the production of prototypes from paper powder for use in the packaging industry. The idea of recycling could thus be strengthened and specifically applied. 3D printed disposable wooden furniture could also play a role, for example a stool as a design object for the exhibition stand, with specific shapes and logos, which could be shredded and recycled after the end of the exhibition.
For which target group do you think additive manufacturing will become more important in the future and where do you see possibilities for better support of this research field?
Henry Burkhardt:
We see potential in 3D printing centres, where companies and private individuals can have designs printed from a wide variety of materials. We also see potential for support in 3D printing with natural materials and basic application research. A further important factor is the strengthening of the transfer between industry and science, in order to convey potential, overcome barriers with regard to project applications from industry and provide a transparent picture of research activities to the outside world.
More information about the company: www.ihd-dresden.com
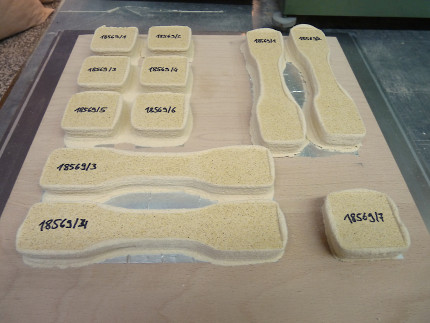
Test specimens produced by selective hot pressing to determine the strength in and parallel to the direction of assembly
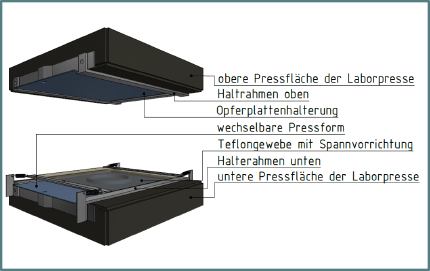
Apparatus for selective hot pressing in the laboratory for the detection of a novel principle for composite generation in additive manufacturing
The interview was conducted by Marlen Krause